Aluminum Alloy Casting
Aluminum alloys contain a high percentage of aluminum alloyed with copper, magnesium, silicon, tin, manganese or zinc. They are lightweight and corrosion-resistant and are the alloy of choice for many aerospace applications due to these properties. Aluminum alloys can be strengthened through either heat treatment or cold-working processes, depending on the alloys.
Precision Investment Casting for Aluminum Alloys
Engineered Precision Casting Company, Inc. provides aluminum alloy casting for prototype to large-scale production runs. We use a master heat system to strictly control our metal inventory and have experience pouring over 75 ferrous and non-ferrous air-melt alloys. For precision investment casting applications requiring additional finishing and services, we also offer heat treatment, non-destructive testing, and more.
Our specialty is casting complex parts for demanding applications. We have extensive experience casting thin-walled and multi-cored aluminum projects for various aerospace customers, utilizing our extensive casting history dating back 70+ years. Contact us to discuss your investment casting project or for assistance selecting the appropriate alloy for your application.
Aluminum Alloy Casting Materials
Aluminum alloys are used for investment casting a wide range of components including those for aircrafts and engines including fittings, housings, levers, valves, impellers, and more. Our aluminum alloy casting material options include:
- A-356 Casting Alloy: contains silicon, magnesium, iron and zinc. It provides excellent corrosion resistance and good weldability and can be heat treated to improve strength.
- A-357 Casting Alloy: is composed of silicon, beryllium, iron, copper, magnesium, titanium, zinc and manganese. It provides high strength and corrosion resistance and can be heat treated to improve the strength characteristics.
- C-355 Casting Alloy: contains silicon, iron, copper, manganese, magnesium, zinc and titanium. It offers excellent corrosion resistance and has good weldability.
- F-357 Casting Alloy: composed of silicon, iron, copper, magnesium, titanium, zinc and manganese. It provides high strength and can be heat treated to improve strength characteristics.
What is Aluminum Casting
Aluminum casting is a kind of metalworking process. By pouring molten aluminum into a precision-designed die or mold. After cooling, the part is removed from the mold. Then get the desired shape casting parts. The mold must be made with precision. Because its quality will have a direct impact on the shape and surface of the finished aluminum alloy casting.
Aluminum alloy castings have properties similar to other aluminum components. It can protect against corrosion.
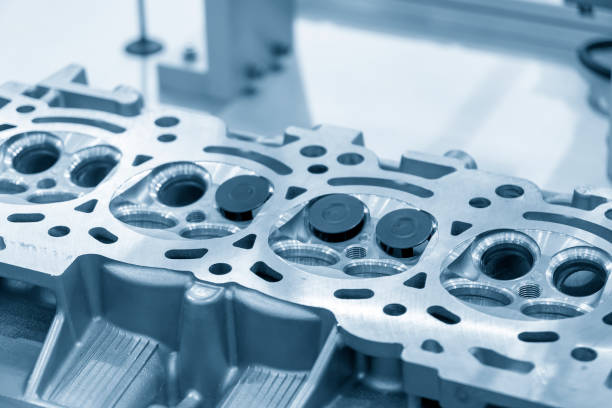
Aluminum Casting Advantages
Aluminum alloy casting is a highly versatile process. Its fluidity, low melting point and rapid heat transfer can result in shorter casting cycles and decreased production time.
Besides it, the additional benefits including
- High strength-to-weight ratio
- Supper chemical stability•Excellent corrosion resistance
- High temperatures Resistance
- Outstanding thermal and electrical conductivity
- Smooth as-cast surface finish
- Complex Shapes
- Less Machining
- Low Cost
Aluminum Casting Process
Casting aluminum is one typical method to get casting parts by pouring molten aluminum into a steel mold. The steel mold has to be precision processed to ensure that the cast piece gets a smooth and refined surface.
There is not only one casting process for aluminum casting. Such as Aluminum die casting, Aluminum permanent mold casting, Aluminum sand casting (green sand and dry sand), Aluminum investment casting, Aluminum continuous casting, etc.
In order to discuss the aluminum casting process, it is necessary to examine the different methods. JC Casting can provide many processes customers would prefer.
Die Casting
Die casting is a process where molten aluminum is forced under pressure into the mold. Aluminum Alloys are used in die casting more extensively than any other alloys metal.
The products produced are exceptionally accurate and need minimal finishing or machining. The process of die casting is rapid, which makes it ideal for mass production of high-volume parts.
There are two types of die casting: low-pressure and high-pressure die casting.
Low-pressure die casting | High-pressure die casting |
---|---|
Good strength values | Lower strength values |
Suitable for automation | Suitable for automation |
Simple die and machine technology | Complicated and expensive dies |
Slower casting cycles | Short casting cycles |
Lower investment and operating costs | High investment and operating costs |
Minimum wall thickness of approximately 3 mm | Suitable for thin-walled components |
Die casting is especially suited to the production of large quantities of relatively small parts. These parts require a minimum amount of finishing and machining. For example, Aluminum die castings weighing up to about 5000 g are common,
This type of casting is often used for mass production of Die casting has short cycle times but high costs for tooling. But castings weighing as much as 50 kg are produced when the high tooling and casting-machine costs are justified.
Sand Casting
The sand casting process involves packing sand around a reusable pattern. The mold has the shape, details, and configuration of the final product. Included in the pattern are risers that allow the molten metal to be poured into the mold. The dimensions of the pattern are slightly larger than the product to account for shrinkage during the cooling process. The sand has the weight and strength to maintain the shape of the pattern and is resistant to interacting with the molten metal.
Sand casting is economical. Because the sand can be reused many times. It is also effective for creating large moldings or those with detailed designs. Upfront tooling costs are low. The single piece is higher, making sand casting suitable for specialized castings over mass production.
Investment Casting
Investment casting is also known as lost wax casting. Start with wax being injected into the mold to create the pattern of the finished product. Assemble the wax piece to form a tree-like configuration. Then dip the tress into a slurry many times to form a strong ceramic shell around the wax shape.
After the ceramic has set and hardened, it is heated in an autoclave to complete the dewax burnout. To achieve the desired temperature of the shell, it is pre-heated before being filled with molten aluminum. It is poured into the sprue and passes through the series of runners and gates into the molds. When the parts harden, the ceramic is knocked off leaving the tree connected parts to be cut from the tree.
Investment casting produces precision parts. Aluminum Investment casting can have walls as thin as 0.40 to 0.75 mm. Investment molding is often used to produce large quantities of intricately shaped parts requiring no further machining. So internal porosity seldom is a problem. Because of porosity and slow solidification, mechanical properties are low.
Investment castings usually are small. It is especially suited to the production of jewelry and parts for precision instruments. It is also used in the aerospace industry.
Aluminum alloys commonly used for investment castings are 208.0, 295.0, 308.0, 355.0, 356.0, 443,0, 514.0, 535.0 and 712.0.
Permanent Mold Casting
Permanent mold casting uses steel or other metal molds and cores. The mold is normally made from gray iron or steel. The mold is shaped into the geometric shape of the designed part with the specifications and shape of the part divided into two halves. Strong castings are formed by pouring aluminum into the mold. Permanent molds are used to create highly repeatable parts with consistency.
Permanent mold casting is used for creating alloy wheels. Aluminum wheels are also lighter than steel wheels, requiring less energy to rotate. They provide greater fuel efficiency, as well as better handling, acceleration, and braking.
Centrifugal Casting
Long shapes of simple cross-sections (such as round, square, and hexagonal rods) can be produced by continuous casting. It can be done in a short, bottomless, water-cooled metal mold.
The casting is continuously withdrawn from the bottom of the mold. Because the mold is water-cooled, the cooling rate is very high.
Continuous casting is a very efficient casting system. Its largest application is the production of ingots for rolling, extrusion, or forging. Cast products are aluminum rods, plates, or pipes up to 0.2×1 m in size.
In previous, we wrote a special blog: 7 Top Aluminum Casting Process It explains 7 top aluminum casting methods’ advantages and disadvantages.
Aluminum Casting Alloys
Cast aluminum alloys Classification is developed by the Aluminum Association of the United States.
Each cast alloy is designated by a four-digit number. Here are eight different aluminum alloys.
The number is from one to eight. The first three numbers show the alloy with which aluminum has been combined.
The first digit indicates the alloy group according to the major alloying element
1xx.x aluminum, 99.0% minimum;
2xx.x copper (4%…4.6%);
3xx.x silicon (5%…17%) with added copper and/or magnesium;
4xx.x silicon (5%…12%);
5xx.x magnesium (4%…10%);
7xx.x zinc (6.2%…7.5%);
8xx.x tin
The second two digits identify aluminum alloy or indicate the alloy purity.
In the alloys of the 1xx.x series the second two digits indicate the level of purity of the alloy. They are the same as the two digits to the right of the decimal point in the minimum concentration of aluminum (in percents). 150.0 means minimum 99.50% of aluminum in the alloy. 120.1 means minimum 99.20% of aluminum in the alloy. In all other groups of aluminum alloys (2xx.x through 9xx.x) the second two digits signify different alloys in the group.
The last digit indicates the product form. casting (designated by “0”) or ingot (designated by “1” or “2” depending on chemical composition limits.)
A modification of the original alloy or impurity limits is indicated by a serial letter before the numerical designation. The serial letters are assigned in alphabetical order starting with A but omitting I, O, Q, and X. (The letter “X” is reserved for experimental alloys).
1000 SeriesThe 1000 series is the purest of the alloys with 99% aluminum content. It is soft and ductile with excellent workability. The 1000 series can endure extreme forming since it hardens slowly. It is easily weldable and performs well during processing.
2000 SeriesThe 2000 series is alloyed with copper-containing 2% to 10% copper and small additions of other elements. The copper enhances the strength and hardness of aluminum. But reduces its ductility and corrosion resistance. Series 2000 is difficult to weld but heat treatable.
Aluminum-copper cast alloys (2xx.x series)
Heat-treatable;
High strength;
Low corrosion resistance (susceptible to stress-corrosion cracking);
Low fluidity;
Low ductility;
Susceptible to hot cracks.
Applications:
Cylinder heads for automotive and aircraft engines, pistons for diesel engines, exhausting system parts.
3000 SeriesThe primary alloying element for series 3000 is manganese. The combination of manganese with aluminum has good corrosion resistance. But is moderately strong. It is a non-reinforced aluminum alloy that has been heat treated. The main benefits of series 3000 is its low density, good plasticity and weldability, corrosion resistance, ductility, and exceptionally smooth finished surface.
Aluminum-silicon-copper/magnesium cast alloys (3xx.x series)
Heat-treatable;
High strength;
Low ductility;
Good wear resistance
Decreased corrosion resistance (in copper containing alloys);
Good fluidity;
Good machinability (in copper containing alloys).
Applications:
Automotive cylinder blocks and head, car wheels, aircraft fittings, casings . parts of compressors and pumps.
4000 Series
The 4000 series is alloyed with silicon, which gives the alloy a low melting point and improves its fluidity. It is one of the more popular casting alloys due to the ease of forming it in its molten state. The 4000 series is used as a welding and brazing filler.
Aluminum-silicon cast alloys (4xx.x series)
Non-heat-treatable;
Moderate strength;
Moderate ductility;
Good wear resistance;
Very good cast properties;
Good corrosion resistance.
Applications:
Pump casings, thin wall castings, cookware.
5000 Series
The 5000 series is alloyed with magnesium. It gives it exceptional tensile strength and formability. It is classified as a high-strength sheet and plate alloy with high weldability. The preference of the 5000 series for sheet metal applications is due to its resistance to acids and alkali corrosion. These characteristics make the 5000 series adaptable to harsh hostile environments.
Aluminum- magnesium cast alloys (5xx.x series)
Non-heat-treatable;
High corrosion resistance;
Good machinability;
Good appearance when anodized;
Moderate cast properties.
Applications:
Sand cast parts.
6000 Series
The 6000 series is alloyed with magnesium and silicon. It gives the alloy strength, mechanical properties, and corrosion resistance. Some versions of the 6000 series are combined with series 4000 and 5000 to enhance the properties of the 6000 series. The processing of the 6000 series requires specialized technologically advanced equipment. This is complex and expensive. Added to its excellent corrosion resistance and oxidation is the ease with which it can be coated and treated as well as its workability.
Aluminum-zinc cast alloys (7xx.x series)
Heat-treatable;
Good dimensional stability;
Good corrosion resistance;
Poor cast properties;
Good machinability (in copper containing alloys).
7000 Series
The 7000 series of aluminum alloys are the strongest and most resilient of the alloys with a strength factor that is two thirds of industrial grade A3 steel. Due to its high hardness, 7000 series have exceptional wear resistance, good mechanical properties, and anode reaction. It is ideal for casting parts that are required to endure a great deal of stress such as aircraft components. Zinc is the alloy of 7000 aluminum, which helps increase its hardness though zinc has the same hardness as aluminum on the Mohs scale.
8000 Series
The primary alloy of the 8000 series is tin with small amounts of copper and nickel. Though this alloy has low strength, it has excellent machinability and wear resistance. The configuration of alloys for the 8000 series changes according to how the product to be produced will be used. Its configuration determines the metal‘s temperature performance, density, and stiffness.
Aluminum-tin cast alloys (8xx.x series)
Non-heat-treatable;
Low strength;
Very good wear resistance;
Good machinability.
Applications:
Monometal (solid) and bi-metal slide bearings for internal combustion engines .slide bearings applications.
How to choose alloy for your applications
Before you start aluminum casting, the aluminum alloy choice is very important. When making the decision of the type of alloy. you can take the below list as a guideline for the properties and characteristics.
- • Corrosion Resistance – excellent in its natural state but changes when alloyed
- • Heat Treating – reduces chemical segregation and improves workability
- • Strength – measured by temper, yield, and tensile strength
- • Formability – ability to undergo plastic deformation
- • Machining – bendability, able to be drilled, resistant to low temperatures
- • Weldability – thermal conductivity, solidification shrinkage, hydrogen solubility, oxide coating
The two charts below outline the distinction between cast alloys and wrought cast alloys. Note that series 600. X does not appear on the cast alloy chart.
Cast Aluminum Grades
Grade | Alloys | Strength | Cracking | Corrosion Resistance | Finishing Capabilities | Weldability |
100.X | Unalloyed | Work Hardening | 1 | 3 | 5 | |
200.X | Cu | Heat Treatment | 4 | 4 | 1To3 | 2 To 4 |
300.X | Mg, Si, Cu | Work Hardening | 1 | 1 | 1 | 3 |
400.X | Si | Undetermined | 4 | 1 | 1 | 3 |
500.X | Mg | Work Hardening | 1 | 1 | 1 | 2 |
700.X | Zn | Heat Treatment | 1 | 4 | 3 | 1 |
800.X | Sn/ Tin, Cu, Ni | Heat Treatment | 5 | 5 | 5 | 5 |
Wrought Alloys Cast Aluminum Grades
Grade | Alloys | Strengthening | Corrosion Resistance | Ability To Be Worked | Weldability | Strength |
1000 | Unalloyed | Work Hardening | 1 | 1 | 3 | 5 |
2000 | Cu | Heat Treatment | 4 | 4 | 5 | 1 |
3000 | Mn | Work Hardening | 2 | 1 | 1 | 3 |
4000 | Si | Undetermined | 4 | 1 | 1 | 3 |
5000 | Mg | Work Hardening | 1 | 1 | 1 | 2 |
6000 | Mg And Si | Heat Treatment | 3 | 2 | 2 | 2 |
7000 | Zn | Heat Treatment | 1 | 4 | 3 | 1 |
8000 | Sn/ Tin, Cu, Ni | Limited | – | – | – | – |
Aluminum Casting Applications
Automotive
The automotive industry is the largest market for aluminum casting. Cast products make up more than half of the aluminum used in cars.
Aluminum cast parts for the automobile industry include Cast aluminum transmission housings and pistons. oil pumps, water pump housings, connectors, transmission parts. .brackets.
The durability and reliability of aluminum cast parts have made them an essential part of auto design improvements and innovations.
Aerospace industry
Aluminum products or Aluminum casting parts are the biggest reliance of the aerospace industry. Especially it’s lightweight and strong. Aluminum parts can reach approximately 80% of the structure of an aircraft.