What Is Sand Casting?
Sand casting is a casting-based process that uses a sand mold. Normally, it relies on silica-based materials. Casting sand consists of finely ground. These spherical grains can be tightly packed together into a molding surface. When a metal is heated to the point that it melts and the chemical composition can be modified. Once the material becomes a liquid property, the molten metal is poured into a sand mold. After cooling, the desired shape of the prototype is manufactured.
The casting is designed to reduce tearing, and cracking by allowing a moderate degree of flexibility and shrinkage during the cooling phase. The process is so popular that it has been used in lots of different industries. Many automotive products, such as housings, and engine blocks are manufactured by this process. Let us have a deep insight into the advantages and disadvantages of sand casting to know more about it.
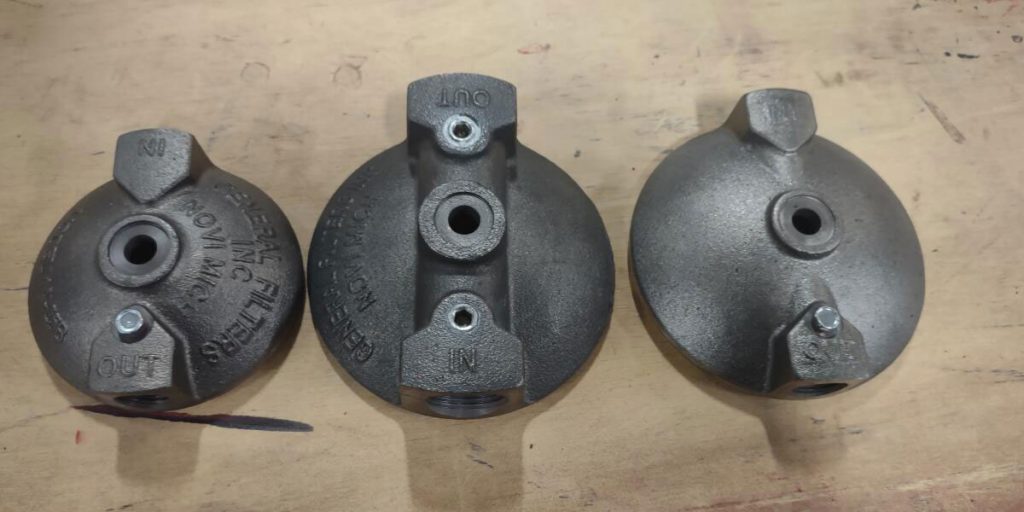
Advantages of Sand Casting
1 Simple production processing
Use common Sand to make a mold or Pattern out. Then pouring into Melton metal liquid into mold or pattern. After cooling down, take the part out. So the production time is short.
2 Time-Saving
Sand casting is a quicker process than the other castings. But sand casting tends to produce rougher parts than other casting types. So we have to consider the additional machining time.
3 Low-Cost Tooling
The sand core is the material to make a sand-casting mold. And it can repeat. So the cost of tooling is relatively low. This makes sand casting can be a better choice for lower-volume needs.
The sand casting patterns (typically wood, plastic, or metal) will have wearing. So the pattern material selection will be decided by the casting parts’ quantity.
4 More metal materials for choosing
One of the main advantages of sand casting is it can be readily produced in nearly any ferrous or non-ferrous alloy.
Some other casting processes will melt and pour super-alloys in a vacuum. But it is not typically done as a sand casting. The non-workable materials must be produced as a casting.
There have many materials that can choose. Like iron, steel, Aluminium, Brass, and so on. Only the sand foundry has this material.
5 Variety on Size, Weight, Shape
Sand castings can be produced in weights from 1kg to several tons.
The shape can be designed by the imagination of the designer. And the internal structures can be cast in place. Because of the casting tolerance limits, it will need machining.
Disadvantages of Sand Casting
1 Low strength
Sand casting is pouring molten material by hand. No pressure. It has a high porosity. So it causes the part inside to be loose. And easy to have porosity defects.
This is different from Gravity Die Casting and High-Pressure Die Casting. So sand casting is best used for smaller, non-weight-bearing workpieces.
2 Low dimensional accuracy
The sand casting process uses a Sand core as a mold. It causes the casting parts’ surface to be rough. The dimension is not precise. Some dimensions have to use CNC to Machine.
3 Rough surface quality
Compared with other casting processes, the sand leaves its texture on the sand casting parts’ surface. It tends to deliver a rougher surface finish. Sand casting parts must be finished as a post-production project.
If you are looking to a workpiece with a machined look. Sand casting is not the best casting choice.
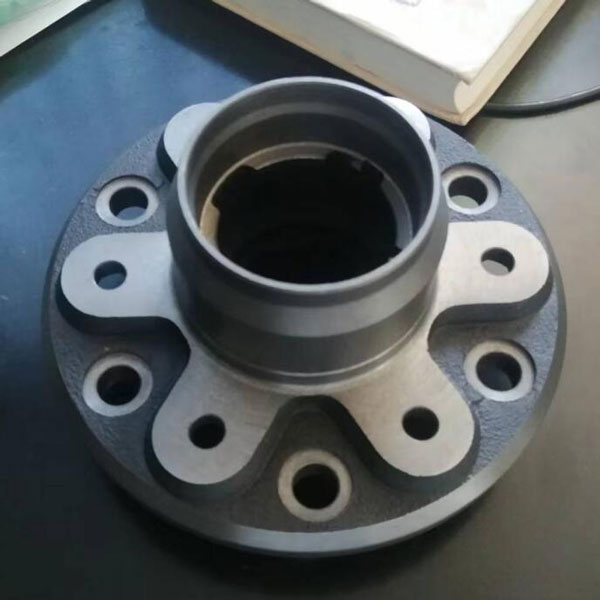
If you do not have a high request on the casting surface finish or no machining, the sand cast is acceptable.
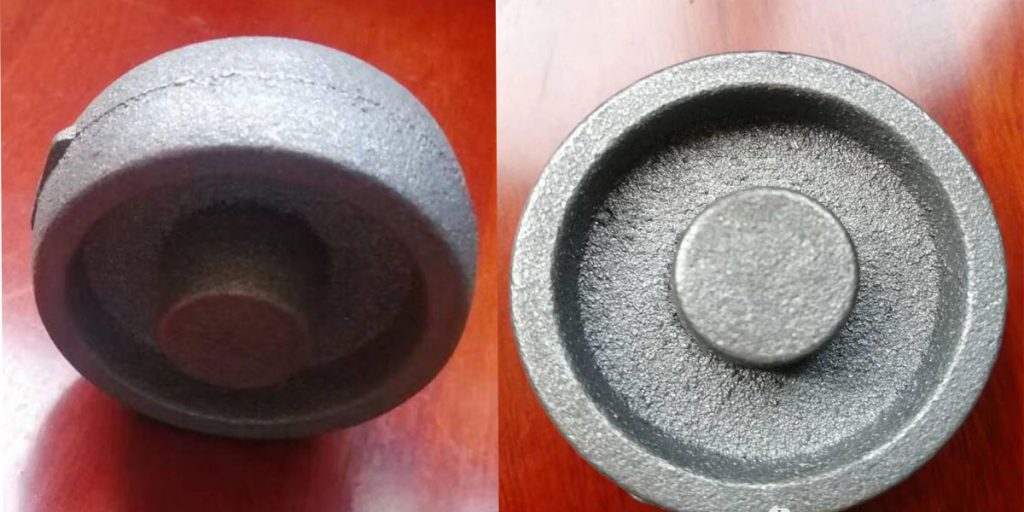
4 More Labor need
Sand casting is labor intensive industry. And Its process is now suitable for large with heavy-size casting. So it needs extra time and labor. A small foundry can not bear it.
5 Mold Limitations
Molds are needed every time. And it can not keep its form when the hot molten metal cools within them. So it needs to rebuild a new mold again.
With the porous nature of sand, a protective coating is a must.
6 Defects Happen
Shrinkage, porosity, metal defects, and surface defects are all possible in sand casting processing.