Aluminum A380, A356, ADC12 are 3 type of aluminum casting raw materials. JC casting foundry often use the 3 grades alloy for die casting, sand casting.
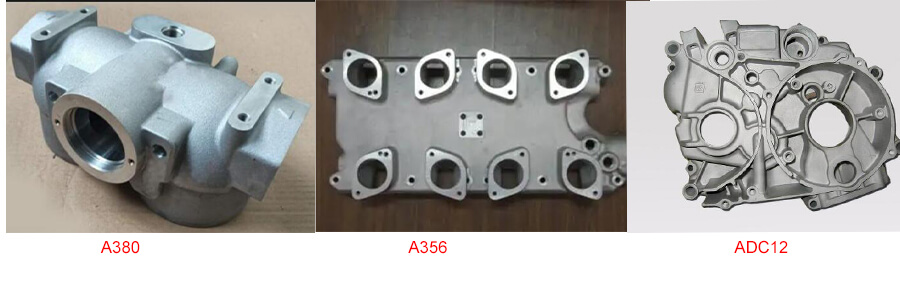
Today, we will introduce the difference between A 380, A356 and ADC12.
Table of Contents
Different alloy compositions
A356 aluminum alloy: The main alloying elements are silicon (Si) and magnesium (Mg). The silicon content is generally around 6.5 – 7.5%. The magnesium content is about 0.2 – 0.4%. This alloy composition design gives A356 good casting properties and mechanical properties. The magnesium element helps improve the strength and toughness of the alloy.
A380 aluminum alloy: The silicon content in the alloy composition is high, approximately between 7.5 – 9.5%. It also contains a small amount of elements such as copper (Cu), iron (Fe), manganese (Mn), and magnesium (Mg). The copper content is around 2 – 4%. The addition of copper can improve the strength and hardness and wear resistance.
ADC12 aluminum alloy: It is a die-cast aluminum alloy of Japanese standard. The main alloying element is also silicon. The silicon content is between 9.6 – 12.0%. In addition, it also contains elements such as copper (1.5 – 3.5%), magnesium (less than 0.3%), and iron (less than 1.3%). The high silicon content gives it good fluidity. So it is suitable for die-casting complex-shaped parts.
Aluminum Alloy Grade | Main alloy elements and content % | Advantage |
A356 | Si:6.5 – 7.5%,Mg:0.2 – 0.4% | The magnesium element is helpful for improving strength and toughness. Good casting and mechanical properties. |
A380 | Si:7.5 – 9.5%,Cu:2 – 4%,Less Fe ,Mn , Mg | The copper element enhances strength and hardness and improves wear – resistance. |
ADC12 | Si:9.6 – 12.0%,Cu:1.5 – 3.5%, Mg :less 0.3%,Fe : less 1.3% | High silicon content, good fluidity, suitable for die – casting complex – shaped parts. |
Differences in mechanical properties
Strength
A356: The tensile strength is moderate. After appropriate heat treatment (such as T6 treatment: solution treatment + aging). Its tensile strength can reach about 200 – 300 MPa. Its strength can meet the part requirements for a certain bearing capacity. For example, car wheels, engine casings.
A380: The tensile strength is high, between 320 – 380 MPa. Due to the strengthening effect of copper element, it has higher strength than A356. It is suitable for manufacturing structural parts that bear large loads. Such as car engine brackets.
ADC12: The tensile strength is comparable to that of A380. Within the range of 300 – 380 MPa. Its strength can ensure that the die-cast parts have bearing capacity during use. It is often used to manufacture automotive parts, electronic equipment casings.
Hardness
A356: It has good hardness. This is due to the magnesium element in its alloy composition. When subjected to external forces such as impact. It can absorb a certain amount of energy without brittle fracture. It is suitable for places that may be impacted.
A380: Due to the high copper content in its alloy composition, its hardness is slightly inferior to A356.
ADC12: The hardness is similar to that of A380. During the die-casting process, due to its good fluidity, the internal structure of the part can be dense. This ensures its toughness. But it is still slightly worse than A356.
Different casting properties
Fluidity
A356: The fluidity is general. It is suitable for casting parts with simple shapes and unregular wall thickness. If casting complex-shaped parts, the pouring temperature needs to be increased.
A380: The fluidity is better. Because of the high silicon content. During the die-casting process, it can fill the mold cavity easily. It is beneficial to manufacture parts with complex shapes and thin walls. Such as electronic equipment casings with fine internal structures.
ADC12: It has excellent fluidity. This is a major advantage as a die-cast aluminum alloy. The high silicon content enables it to quickly and smoothly fill every corner of the mold during die-casting. So parts with high precision and complex shapes can be die-cast. Like small die-cast parts of car engines.
Shrinkage rate
A356: The shrinkage rate is relatively small. The volume change is not significant during solidification. This helps ensure the dimensional accuracy of the casting. Especially for some parts with high dimensional accuracy requirements. Such as small aluminum alloy castings in the aerospace field.
A380: The shrinkage rate is slightly larger than that of A356. During the die-casting process, its shrinkage characteristics need to be considered. Reasonably design the shrinkage allowance of the mold to ensure that the final part size meets the requirements.
ADC12: The shrinkage rate is similar to that of A380. When die-casting complex-shaped parts, the mold and process parameters need to be designed. It will according to its shrinkage characteristic. This can prevent the parts from having dimensional deviations or deformations.
Differences in application
A356: Widely used in the casting of car wheels and aerospace parts. For car wheels, its good mechanical properties and low density can reduce vehicle weight. In the aerospace field, its performance can meet the manufacturing requirements of some small parts.
A380: Mainly used in manufacturing automotive engine parts, electronic equipment casing. In automotive engine parts, its high strength can withstand various loads generated . For electronic equipment casings, good die-casting performance can produce beautiful-looking casings.
ADC12: Applied to die-cast parts in the automotive and electronic industries. In the automotive industry, it is used to manufacture complex die-cast parts. Such as transmission cases. In the electronic industry, it is often used to manufacture casings of electronic products. Such as mobile phones and computers. Improve good die-casting performance to meet appearance requirements.
Differences in casting costs
Raw material cost
A356: Its raw material cost is stable. Affected by the price fluctuations of raw materials such as silicon and magnesium. Relatively simple in alloy composition. Higher requirements for the purity of raw materials. Especially, the control of impurities is strict. This also affects its raw material procurement cost to a certain extent.
A380: The silicon content in the alloy composition is high. Due to its complex alloy composition containing copper elements with high prices. Higher requirements for impurity control. So its raw material cost is higher than that of A356.
ADC12: The main alloying element is silicon. In addition, it also contains elements such as copper, magnesium, and iron. Its silicon content is high. Greater dependence on silicon. Material cost is high. Its raw material cost is close to that of A380.
Casting cost
A356: The melting process is simple. No special melting process and equipment are required. But the control of composition is high. Precise batching and melting process control are required. This increases the labor cost and equipment maintenance cost of melting.
A380: Due to the complex proportion of various alloying elements, the melting is difficult and the cost is high.
ADC12: There are mature technologies and experiences in melting process and equipment. Some costs can be reduced.
Casting process cost
A356: Commonly used in gravity casting and low-pressure casting.
A380: Commonly used in die-casting process.
ADC12: Mainly used in die-casting process. Similar to A380, it requires equipment such as high-pressure die-casting machines and complex molds.
Post-treatment cost
A356: Usually requires post-treatment processes such as heat treatment and surface treatment.
A380: The post-treatment process is similar to that of A356.
ADC12: The post-treatment process mainly includes deburring, shot blasting, surface treatment. Due to the characteristics of the die-casting process, there may be some defects. Such as pores and shrinkage cavities on the casting surface. Additional treatment is required. This increases the workload and cost of post-treatment.
In conclusion, the casting cost of A380 is usually the highest, followed by ADC12, and A356 is relatively low. But, the specific casting cost will also be affected by various factors. Such as production batch, production equipment, and process requirements.
If you have any A380 casting, A356 Aluminum casting or ADC12 alloy casting inquiry, welcome contact us!