Aluminum Casting
JC Casting is a Customize aluminum casting company with ISO Certificate in China. We focus on aluminum Casting production in different casting processes: Investment casting, sand casting, die casting.
What is Aluminum Casting?
Aluminum casting is a kind of metalworking process. By pouring molten aluminum into a precision-designed die or mold. After cooling, the part is removed from the mold. Then get the desired shape casting parts. The mold must be made with precision. Because its quality will have a direct impact on the shape and surface of the finished aluminum alloy casting.
Aluminum alloy castings have properties similar to other aluminum components. It can protect against corrosion.
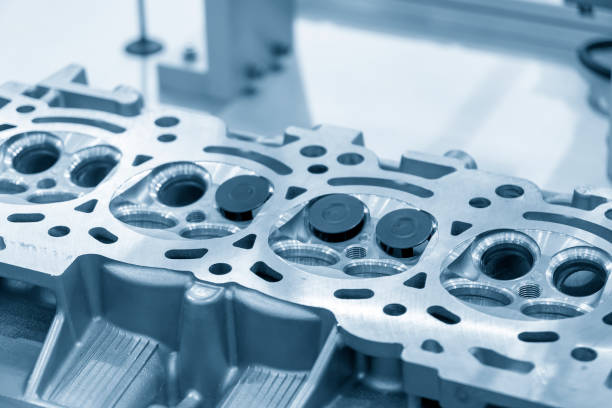
Aluminum Casting Company, Process
JC Casting is an aluminum casting company in China. We have our own foundry and machining workshops.
For aluminum casting, there is not only one casting process for aluminum casting. Such as Aluminum die casting, Aluminum permanent mold casting, Aluminum sand casting (green sand and dry sand), Aluminum investment casting, Aluminum continuous casting, etc.
Features
Aluminum alloy casting is a highly versatile process. Its fluidity, low melting point and rapid heat transfer can result in shorter casting cycles and decreased production time. Besides it, the additional benefits including
- High strength-to-weight ratio
- Excellent corrosion resistance
- Outstanding thermal and electrical conductivity
- Complex Shapes Available
- Less Machining, Low Cost
Aluminum Alloy Casting
Aluminum alloys contain a high percentage of aluminum alloyed with copper, magnesium, silicon, tin, manganese or zinc. They are lightweight and corrosion-resistant and are the alloy of choice for many aerospace applications due to these properties. Aluminum alloys can be strengthened through either heat treatment or cold-working processes, depending on the alloys.
Precision Investment Casting for Aluminum Alloys
Engineered Precision Casting Company, Inc. provides aluminum alloy casting for prototype to large-scale production runs. We use a master heat system to strictly control our metal inventory and have experience pouring over 75 ferrous and non-ferrous air-melt alloys. For precision investment casting applications requiring additional finishing and services, we also offer heat treatment, non-destructive testing, and more.
Our specialty is casting complex parts for demanding applications. We have extensive experience casting thin-walled and multi-cored aluminum projects for various aerospace customers, utilizing our extensive casting history dating back 70+ years. Contact us to discuss your investment casting project or for assistance selecting the appropriate alloy for your application.
Aluminum Alloy Casting Materials
Aluminum alloys are used for investment casting a wide range of components including those for aircrafts and engines including fittings, housings, levers, valves, impellers, and more. Our aluminum alloy casting material options include:
- A-356 Casting Alloy: contains silicon, magnesium, iron and zinc. It provides excellent corrosion resistance and good weldability and can be heat treated to improve strength.
- A-357 Casting Alloy: is composed of silicon, beryllium, iron, copper, magnesium, titanium, zinc and manganese. It provides high strength and corrosion resistance and can be heat treated to improve the strength characteristics.
- C-355 Casting Alloy: contains silicon, iron, copper, manganese, magnesium, zinc and titanium. It offers excellent corrosion resistance and has good weldability.
- F-357 Casting Alloy: composed of silicon, iron, copper, magnesium, titanium, zinc and manganese. It provides high strength and can be heat treated to improve strength characteristics.
Aluminum Casting Process
Casting aluminum is one typical method to get casting parts by pouring molten aluminum into a steel mold. The steel mold has to be precision processed to ensure that the cast piece gets a smooth and refined surface.
In order to discuss the aluminum casting process, it is necessary to examine the different methods. JC Casting can provide many processes customers would prefer.
- Die Casting: There are two types of die casting: low-pressure and high-pressure die casting.
- Sand Casting
- Investment Casting
- Permanent Mold Casting
- Centrifugal Casting
In previous, we wrote a special blog: 7 Top Aluminum Casting Process It explains 7 top aluminum casting methods’ advantages and disadvantages.
Aluminum Casting Alloys
Cast aluminum alloys Classification is developed by the Aluminum Association of the United States.
Each cast alloy is designated by a four-digit number. Here are eight different aluminum alloys.
The number is from one to eight. The first three numbers show the alloy with which aluminum has been combined.
Cast Aluminum Grades
Grade | Alloys | Strength | Cracking | Corrosion Resistance | Finishing Capabilities | Weldability |
100.X | Unalloyed | Work Hardening | 1 | 3 | 5 | |
200.X | Cu | Heat Treatment | 4 | 4 | 1To3 | 2 To 4 |
300.X | Mg, Si, Cu | Work Hardening | 1 | 1 | 1 | 3 |
400.X | Si | Undetermined | 4 | 1 | 1 | 3 |
500.X | Mg | Work Hardening | 1 | 1 | 1 | 2 |
700.X | Zn | Heat Treatment | 1 | 4 | 3 | 1 |
800.X | Sn/ Tin, Cu, Ni | Heat Treatment | 5 | 5 | 5 | 5 |
Wrought Alloys Cast Aluminum Grades
Grade | Alloys | Strengthening | Corrosion Resistance | Ability To Be Worked | Weldability | Strength |
1000 | Unalloyed | Work Hardening | 1 | 1 | 3 | 5 |
2000 | Cu | Heat Treatment | 4 | 4 | 5 | 1 |
3000 | Mn | Work Hardening | 2 | 1 | 1 | 3 |
4000 | Si | Undetermined | 4 | 1 | 1 | 3 |
5000 | Mg | Work Hardening | 1 | 1 | 1 | 2 |
6000 | Mg And Si | Heat Treatment | 3 | 2 | 2 | 2 |
7000 | Zn | Heat Treatment | 1 | 4 | 3 | 1 |
8000 | Sn/ Tin, Cu, Ni | Limited | – | – | – | – |
Aluminum Casting Applications
Automotive
The automotive industry is the largest market for aluminum casting. Cast products make up more than half of the aluminum used in cars.
Aluminum cast parts for the automobile industry include Cast aluminum transmission housings and pistons. oil pumps, water pump housings, connectors, transmission parts. .brackets.
The durability and reliability of aluminum cast parts have made them an essential part of auto design improvements and innovations.
Aerospace industry
Aluminum products or Aluminum casting parts are the biggest reliance of the aerospace industry. Especially it’s lightweight and strong. Aluminum parts can reach approximately 80% of the structure of an aircraft.
Product Description Of Our Aluminum Aluminum casting Services
- Wide range of machining aluminum materials:Aluminum 6061, Aluminum 2024, Aluminum 5052, Aluminum 6063,Aluminum 7050,Aluminum 7075,Aluminum MIC-6
- Custom Colors:Black, Natural, Blue, Green and different colors as your requirements
- Surface Finishing:Sand blasting, shot blasting, polishing, anodizing, oxidation, electrophoresis, chromate, powder coating and painting
- Various Aluminum CNC Machining Process: CNC aluminum turning, CNC aluminum drilling
- Aluminum CNC Machining Applications:Aluminum CNC parts can be applied to automotive, electrics, military, medical, aircraft, power generation, aerospace, and industrial engineering
Typical Aluminum Casting Products Gallery
investment, sand casting, die casting, CNC casting
If you have an inquiry for aluminum castings, you can tell us your need or send us a drawing.
Our professional sales engineer will reply to you within 12 hour
Customized Aluminum Casting Manufacturer
JC Casting is a Customize aluminum casting company with ISO Certificate in China. We focus on aluminum Casting production in different casting processes: Investment casting, sand casting, die casting.
Aluminum casting is a kind of metalworking process. By pouring molten aluminum into a precision-designed die or mold. After cooling, the part is removed from the mold. Then get the desired shape casting parts. The mold must be made with precision. Because its quality will have a direct impact on the shape and surface of the finished aluminum alloy casting.
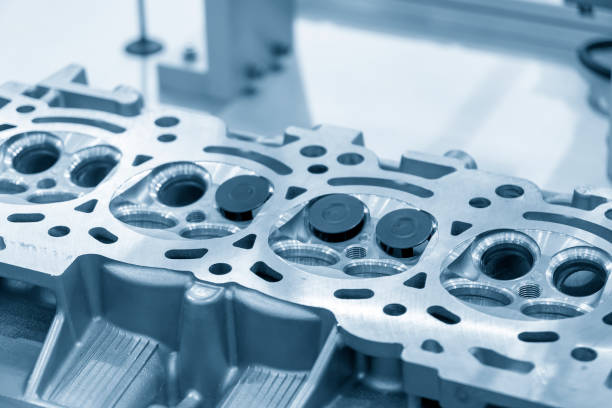
PROCESSING
- Aluminum die casting
- Aluminum permanent mold casting
- Aluminum sand casting (green sand and dry sand)
- Aluminum investment casting
- Aluminum continuous casting
ADVANTAGES
- High strength-to-weight ratio
- Excellent corrosion resistance
- Outstanding thermal and electrical conductivity
- Complex Shapes Available
- Less Machining, Low Cost
Applications
- Aerospace Industry
- Food
- Automotive