Investment Casting Process
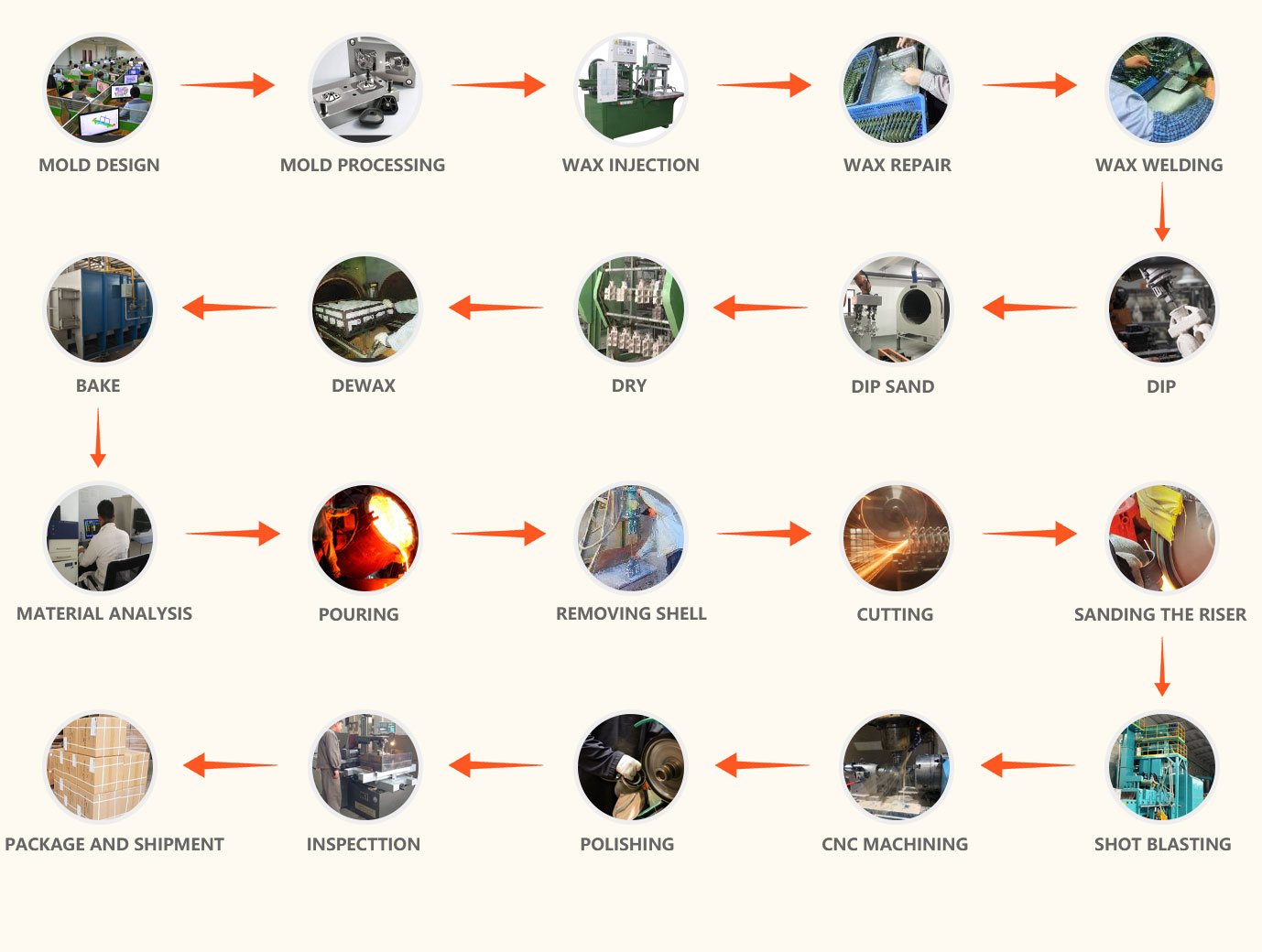
Step 1: Tooling Making
Tool making is the primary step in investment casting. This is the basis for obtaining the correct product. These tools or templates are precision machined in CNC centers. Customers typically charge for tools to order new product samples.
Step 2: Wax Injection and Pattern Assembly
Casting the model as a wax module after casting. The wax pattern is obtained by entering waxes on the model. The output will be a model with the same dimension as the desired product. Then repeat the injection operation for more wax models. Then collect this modular wax model and collect the drue. Finally, hang these pattern assemblies at room temperature to dry.
Step 3: Shell Coating
In the shell coating step or process, the version meeting is immersed in a ceramic and lined with a refractory material. The technique is to be done repeatedly in numerous instances till regular thickness and power are attained. The ceramic shell is then completed and positioned in managed atmospheric surroundings earlier than drying.
Step 4: Dewaxing
Put the shells in a steam autoclave and heat them up quickly in this way wax is melted and flowed through the gate and poured at high temperature. The ceramic shell must be fired to preheat the mold before casting and firing the last remaining material of the model. Typically in the range of 1600-2000 degrees Fahrenheit. This is why the industry called investment casting is also named “lost wax casting”.
Step 5: Casting or Pouring
After the dewaxing process, the steel or aluminum ingot is melted to a liquid state. After which pour liquid metal into the spruce and let it cool slightly at room temperature. Casting is a key step in the entire investment casting process.
Step 6: Shell Removing
After cooling has been done, the ceramic shell is then broken and individual castings are cut from the sprue. The next thing to it tt is then ground to remove excess metal from the casting body.
Step 7: Heat Treatment
When it comes to heat treatment is usually performed after casting is completed. This process improves the mechanical properties of the casting blank. The main heat treatment procedures are normalizing, tempering, annealing, quenching and tempering, carburizing. Additional heat treatment means another cost. Talking about heat treatment requirements they are considered in advance and additional costs are needed to be accounted for.
Step 8: Shot Blasting/Sand Blasting
To eliminate scale and enhance floor finish quality, funding castings are shot blasted or sandblasted with small metallic balls. Therefore, each foundry ought to be geared up with a shot blasting machine.
9. Anti-rust Oil Painting & Surface Treatments
Castings are immersed in anti-corrosion water or oil to prevent corrosion. Other surface treatments such as spray paint and galvanizing can also be performed at this stage.
10. Quality Inspection
Inspection is also a quality control step in investment casting. The QC will do a dimensional inspection, 100% surface inspection, internal defect inspection, and other inspection work according to product requirements. All products must be tested before they can be sent to customers.
11. Package
We usually pack our investment castings in special bags and then put them in cartons and standard wooden cases. We can also provide customized packaging services according to customers’ requirements.