What is a Foundry
How to define a foundry? A foundry is a factory or workshop that specializes in casting production. It heats metals into a liquid state. Then, the molten metal liquid is poured into a pre-designed mold cavity. After cooling, the metal products with the required shape and size are obtained. In short, a foundry is a place for metal forming processes. It bears the mission of transforming metal materials into products with specific shapes and properties.
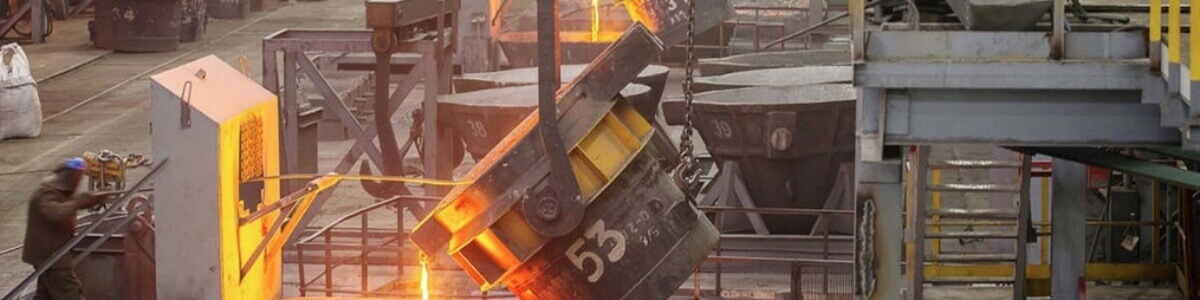
A foundry has a series of professional equipment and technicians. It covers many processes: from the preparation of raw materials, smelting, molding, pouring to the cleaning and inspection of castings. The castings has a widely used in industries. Such as automobiles, aerospace, machinery manufacturing, construction, and ships. It is one of the fundamental supports of modern industry.
JC Casting is a foundry with lost wax investment casting, sand casting, die casting and CNC service.
Classification of Foundries
Foundries can be categorized into various types based on different classification criteria. The following are some of the common ways of categorization:
Classification by Casting Process
1. Sand Casting foundry
This is the most traditional and widely used type of casting foundry. It uses the sand to make sand molds, and then pours in liquid metal to cast. Its equipment is simple, and the cost is low. It is suitable for all kinds of batch production. Since the accuracy of the sand mold is not very high, the surface quality and dimensional accuracy of the castings are just so-so.
2. Metal Casting foundry
The mold is made of metal. The liquid metal is poured into the metal mold by gravity casting. The castings will have high dimensional accuracy, good surface quality, and high production efficiency. But the cost is quite high. It is suitable for batch production, not for single or small-batch production.
3.Pressure Casting foundry: Also called a die casting foundry.
It is a process where liquid or semi-liquid metal is filled into the mold cavity at high speed under high pressure and then solidifies quickly. The die castings have high accurate dimension, smooth surface, and high production efficiency. It is often used to make thin-walled, complex-shaped casting。 Such as the cylinder blocks and cylinder heads of car engines. But the investment cost and mold requirements are high.
4.Centrifugal Casting foundry
The Liquid metal is poured into a mold that is rotating at high speed. The metal fills and solidifies under the centrifugal force. It is suitable for making tubular and ring-shaped castings (such as cast iron pipes and copper sleeves). The structure of the castings is dense, and their performance is good. Also, no core is needed.
5.Investment Casting foundry: Also known as lost-wax casting.
It can make complex castings with high accuracy size and smooth surface quality. It is widely used in the precision machinery industries.
Classification by Production Scale
1.Large Casting foundry
The annual production capacity is ≥ 5000 tons. It has advanced equipment and management. It can make large and complex castings. such as ship propellers and heavy machinery parts. It has a high technical level and advanced production processes. It can do research, development, and innovation. But the foundry investment cost is high in the equipment, the site, and the workers.
2.Medium-sized Casting foundry
The annual output capacity is between 1000 and 5000 tons. It pays attention to both quality and efficiency. It has some ability to do technical research and development. It can meet different needs. It can take both batch orders and small or medium-sized custom orders. It is quite flexible in the market.
3.Small Casting foundry
The annual production output capacity is less than 1000 tons. It will be small in scale. And the equipment is simple. It focuses on making small or small-batch castings (such as machine parts and handicrafts). It can respond to needs quickly. The production cycle is short, and it has a cost advantage. It is an important supplier for the local market and small and medium-sized companies.
Foundry Casting Processes
The basic working process of a casting foundry is different depending on the casting process. But generally, it has the following main steps:
1.Production Preparation
Design the casting drawings according to the inquiry. Make a casting process: such as sand casting, investment casting, or pressure casting. Then Decide on the molding materials, smelting, and pouring plans. Raw Material Preparation: Prepare and check the needed metal raw materials. Such as cast iron, cast steel, and aluminum alloy. To make sure they meet the requirements. Prepare the molding materials: such as molding sand, core sand, and binders. Mold Making: Make molds according to the size of the castings (for example, make wooden or metal molds for sand casting, and make master molds for investment casting). Make sure the molds are accurate to get good-quality castings. Make sure the molds are accurate to get good-quality castings.
2.Molding and Core Making Molding
Use molding sand and other materials to make a mold on the pattern to form the pouring cavity.
Core Making: Use core sand and binders to make cores. After the cores are solidified, put them into the mold. They can form the inner holes or complex parts of the castings.
3.Smelting and Pouring
Put the metal raw materials into the smelting equipment (such as a cupola furnace or an electric furnace) to melt them. Make sure the temperature and composition are right. During smelting, deoxidize and remove gas from the metal liquid to make it better. Pouring: Pour the metal liquid into the mold cavity. Control the pouring speed, temperature, and amount carefully to make sure the cavity is filled completely and avoid problems like air holes and shrinkage.
4.Cooling and Solidification
After pouring, the metal liquid cools down and solidifies into a casting. During the cooling process, control the cooling speed and time well to get the right structure and performance of the casting.
5.Shakeout and Cleaning
Shakeout: After the casting is solid,you can take it out and remove the molding sand and cores by removing the shell. You can do the step by hand or with a machine. Cleaning: Clean the casting to remove the sand which is stuck on the casting surface and the burrs. There are many Cleaning methods: mechanical cleaning. (such as shot blasting, tumbling, and grinding), chemical cleaning. (such as pickling and alkaline cleaning). Hydraulic cleaning.
6.Inspection and Post-treatment Inspection:
Check the casting appearance and measure its size. do non-destructive testing.such as flaw detection and ultrasonic testing. Test its mechanical properties. Such as tensile testing and hardness testing. Make sure the casting meets the design requirements and quality standards.
7.Post-treatment
According to the casting requirements or application, do post-treatment on the qualified casting. This can include heat treatment.Such as annealing, normalizing, quenching, and tempering. Surface treatment: electroplating, painting, and passivation. This can improve the structure and performance of the casting. Make it more resistant to corrosion and look better.
Foundry Equipment and Facilities
The casting process of a foundry is different depending on the equipment and facilities. But generally, it includes the following common types:
1. Smelting Equipment
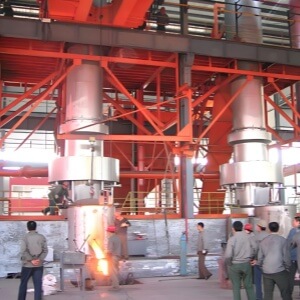
Cupola Furnace
It is a device to smelt cast iron. It uses coke as fuel to melt pig iron, scrap steel, and other materials. It has a high melting rate and low cost。 It is good for making cast iron parts in huge quantities.
Electric Arc Furnace
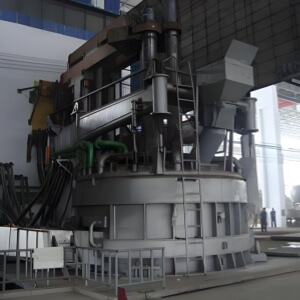
It melts the metal by the heat of the arc between the electrodes and the materials. It can smelt all kinds of iron and steel materials, including ordinary steel and special alloy steel. It heats up fast, controls the temperature well, and can control the metal composition easily.
Induction Electric Furnace
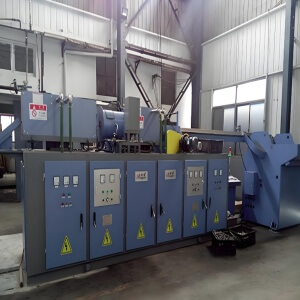
It uses electromagnetic induction to make heat and melt the metal. There are medium-frequency electric furnaces. It is widely used for smelting non-ferrous metals。Such as copper and aluminum and special steel. It has high heating efficiency, little pollution, and loss of alloy elements.
2.Molding and Core-making Equipment
Molding Machine
It is special equipment for sand casting. There are vibration-pressure types, shooting-pressure types, and static-pressure types. It is used to compact the sand mold and take out the pattern. It can make the work more efficient and the quality better.
Core-making Machine
It is used to make cores. Common ones are hot-box core-making machines and cold-box core-making machines. The hot-box one makes the binder in the core sand solidify by heating. The cold-box one uses a gas catalyst to make the core sand harden quickly at room temperature.
Molds
There are patterns for molding and core boxes for making cores. Patterns are usually made of wood or metal (such as aluminum alloy and cast iron) and are used to form the outside shape of the casting. Core boxes are used to make cores, which form the inner holes or complex parts of the casting.
3.Pouring Equipment
Ladle
It is used to hold and carry the metal liquid for pouring. There are different kinds of ladles. Such as hand-carried ladles and crane ladles. You can choose the right one according to the production scale and pouring needs.
Pouring Machine
It can pour automatically. It can control the pouring amount and speed accurately. It can make the pouring more accurate and efficient and reduce the influence of people on the quality of the casting.
4.Cleaning Equipment
Shot Blasting Machine
It cleans the sand and burrs on the surface of the casting by throwing shots at high speed. There are drum types, crawler types, etc. It is suitable for cleaning castings of different shapes and sizes.
Sandblasting Machine
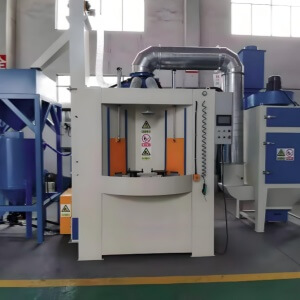
It uses high-pressure air to spray sand grains to clean the casting and treat its surface. It can clean complex-shaped castings that are hard for the shot blasting machine to clean. It can also make the surface of the casting rougher to help the later coating stick better.
5.Grinding Equipment
Such as grinding wheels and angle grinders. They are used to grind and fix the casting locally, to remove the protruding or uneven parts on the surface and make the surface meet the roughness and size requirements.
6.Detection Equipment
Hardness Tester
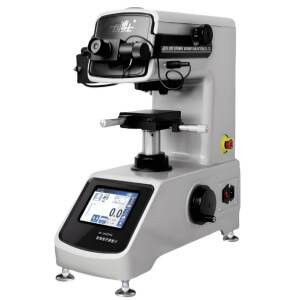
It is used to measure the casting hardness. There are method of Brinell hardness testers, Rockwell hardness testers, and Vickers hardness testers. The hardness is an important standard of the quality and performance of the casting.
Flaw Detector
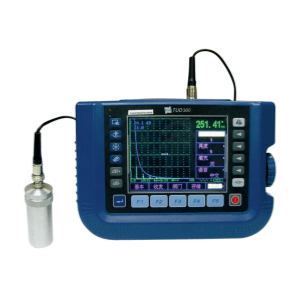
There are ultrasonic flaw detectors, magnetic particle flaw detectors, and penetrant flaw detectors. They are used to find the internal defects and surface defects of the casting.Such as . Like cracks, air holes, and slag inclusions. This can make sure the casting is safe and reliable in using.
Spectral Analyzer
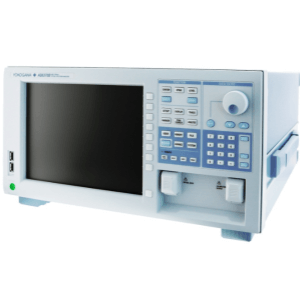
It is used to analyze the chemical composition of the metal material. It can analyze the composition of the metal liquid during smelting to make sure the chemical composition of the casting is right.
7.Other Auxiliary Equipment and Facilities
Dust Removal Equipment
Such as bag dust collectors and cyclone dust collectors. They are used to collect and deal with the dust made during the casting process to protect the environment and the health of the workers.
8. Lifting and Transportation Equipment
Such as cranes, electric hoists, and forklifts. They are used to lift and carry raw materials, molds, and castings to make the material transportation faster foundry
9.Buildings and Workshop Facilities
There are production workshops, warehouses, offices, and other buildings, as well as facilities like ventilation, lighting, and power supply. They provide the necessary place and working conditions for casting production.
In short, a casting foundry is an important place for shaping metal. Through different processes and production methods, it makes all kinds of castings. Among them, the investment casting foundry, with its special technical advantages, helps the precision casting industry develop.