Manufacturing
JC Casting is a casting manufacturer in China. We can provide 5 main casting manufacturing methods: investment casting (Silica Sol lost wax investment casting and waster glass investment casting), sand casting, die casting and CNC machining.
The 5 casting manufacturing methods in JC Casting Factory.
1–Investment casting
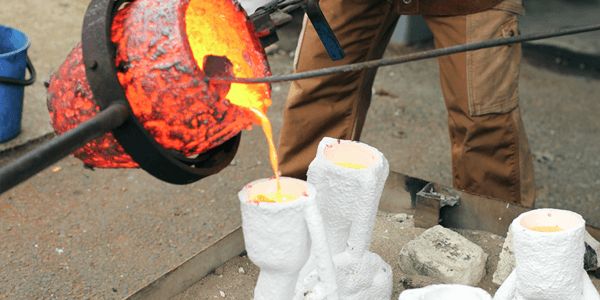
Investment casting is a very old manufacturing method. It refers to the general term for the process of obtaining precise size casting. Its products are precise, complex and close to the final shape of parts. Compared to traditional sand casting, investment casting results in more accurate casting size and better surface finish. It includes wax mold casting, ceramic mold casting, metal mold casting, and so on. They can be used directly with little or no post-processing.
Advantages of Investment Casting
- Superior Surface Finish
- Variety of Materials
- Complex Design,Closer to Finished Part Designs
- Tight Tolerances
- Competitive Tooling Costs
Investment Casting Types:
JC Casting can provide Silca Sol lost wax Investment casting process and water glass lost wax investment casting process.
2–Sand Casting
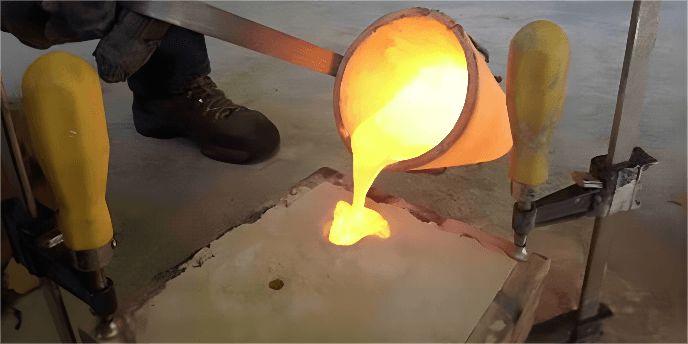
Sand casting is also known as sand molded casting. It is a metal casting process characterized by using sand as the mold material. The sand casting part refers to an object produced by the sand casting process. Sand castings are produced in sand casting foundries.
In the market, more than 61% of all metal castings are produced via the sand casting process. Sand casting is the most widely used metal casting method.
Molds made of sand are relatively cheap. It is sufficiently refractory even for steel foundry use.
Advantages of Sand Casting
- Lower costs for low-volume production runs
- Suitability for fabricating large components
- Ability to use ferrous or non-ferrous metals
- Shorter lead time compared to other processes
3–Die Casting
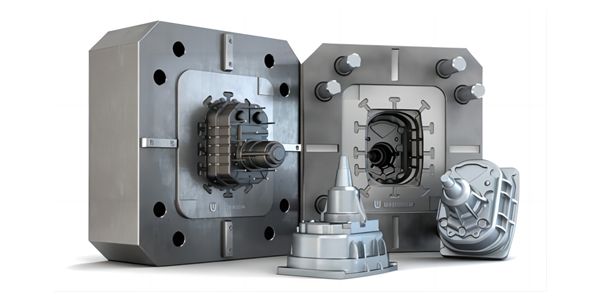
Die casting is a metal casting process. It is characterized by the use of a mold cavity to apply high pressure to melted metal. Molds are usually machined with stronger alloys. The making of die cast parts is relatively easy, and generally requires only four major steps. They are preparation, filling, injection, and sand shakeout. Die casting has a more positive significance for aluminum alloy automobile wheels, frames and other components with higher strength impact-resistant materials.
Advantages of Die Casting
- Excellent dimensional accuracy
- Avoid secondary mechanical processing
- Fast production speed
4–CNC Machining
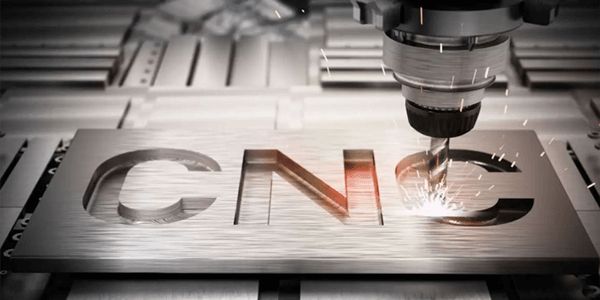
CNC machining definition is that it is a process of subtractive manufacturing. It uses computer and machine tools to remove layers of material from a blank or cast to produce a custom-designed part. CNC (Computerized Numerical Control) machining controls a range of complex machinery. Such as grinders, lathes, and turning mills. They are used to cut, shape, and create different parts and prototypes
The CNC process is suitable for a wide range of materials. Including metals, plastics, wood, glass, foam, and composites, and finds application in a variety of industries. Such as large CNC machining, machining of parts and prototypes for telecommunications, and CNC machining aerospace parts. They need higher tolerances than other industries. So, it is important for a manufacturer or factory to have knowledgeable CNC machinists and programmers in the industry to operate this high-tech machinery.
JC Casting has 12 sets of CNC machines and 5 engineers, 120 staff.
PS:
CNC machining definition vs the CNC machine definition: One is a process and the other is a machine.
CNC Machining Produces Little to No Waste
Advantages of CNC Machining
- Zero Defects and Greater Accuracy
- Faster and Efficient Production
- Complex designs available
- One operator can supervise more than one machine at a time
Besides the above 5 Casting Manufacturing Methods, we can also make by lost foam casting processing for huge casting parts. Such as pump casting, the impeller casting.