Stainless Steel Casting
What is Stainless Steel Casting?
Stainless steel casting, also known as lost wax investment casting, is a precision casting process for manufacturing stainless steel parts. In this process, a wax pattern is made to the exact shape of the desired part. This wax pattern is then coated with multiple layers of refractory materials to form a shell. When the shell is hardened, the wax is melted out, leaving a hollow cavity. Molten stainless steel is then poured into this cavity. As the metal cools and solidifies, it takes on the shape of the original wax pattern. Then get the stainless steel casting parts!
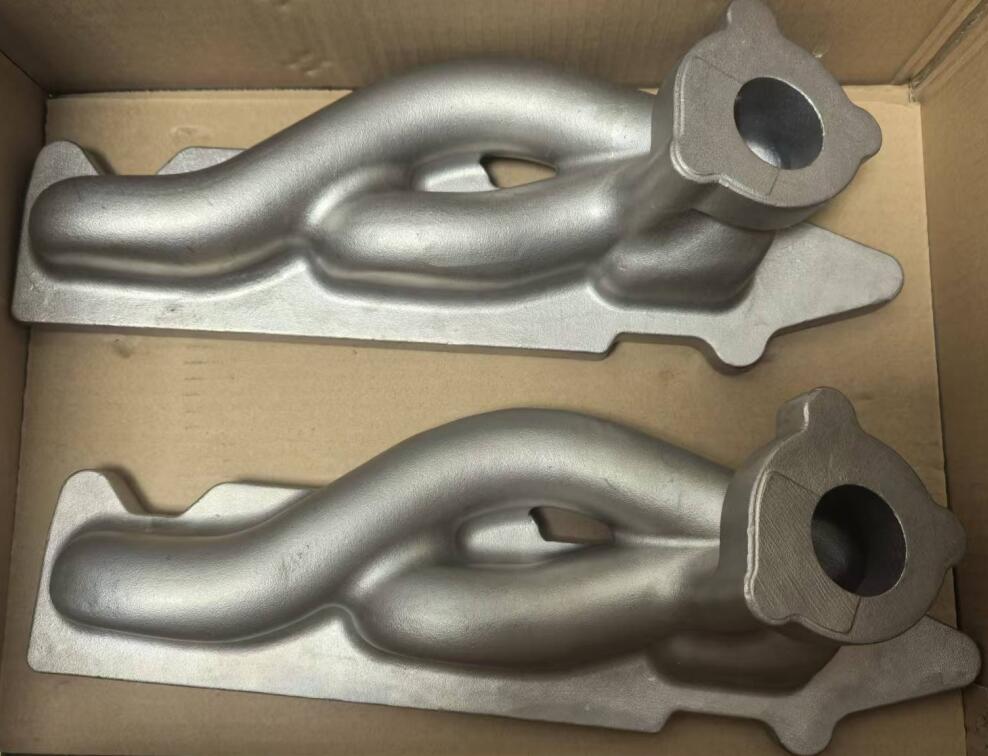
JC Casting is a Stainless Steel Casting Manufacturer in China. We have Stainless Steel Casting foundry with different stainless steel grades.
Advantages of Stainless Steel Casting
Stainless steel castings have the following advantages:
- Strong corrosion resistance
It can be used for a long time in harsh chemical environments. For example, it can resist the erosion of corrosive media such as acids, alkalis, and salts. It is widely used in fields : chemical industry, food processing, and marine engineering.
- Good high-temperature performance
It can maintain its strength and stability in high-temperature environments. It can be used in high-temperature environments . Such as oil refining, coal-fired power generation, and aerospace.
- High strength
It can withstand large loads in various engineering environments. For example, in fields such as mechanical equipment, automobile manufacturing, and building structures.
- Good wear resistance:
It can withstand the test of friction and wear. In mechanical transmission parts and pump valve parts, stainless steel castings can have a long service life.
- Good processability
It can be processed by various casting, stamping, welding, and machining processes.
- High dimensional accuracy
It can reach CT4-6 level. The deviation of the casting’s size from the design requirements is small. It can meet the manufacturing needs of high-precision parts.
- Good surface quality
The surface finish is high. It is beneficial to reduce fluid resistance. For example, in applications such as pipes and valves.
- Strong designability
According to different needs and design requirements, castings with complex shapes and unique structures can be manufactured.
- Good environmental protection
It is a recyclable material. The surface is smooth and not easy to breed bacteria. It is widely used in food, medicine, and other fields.
Here, we have a full article to introduce the Advantages and disadvantages of Stainless Steel Casting. Kindly view it
Stainless Steel Casting Applications
Stainless steel investment castings have a wide range of uses, mainly in the following areas:
I. Industrial field
1. Chemical industry: Used in the manufacture of reactors, tanks, pipelines, valves and other equipment. tIt can resist strong acids, alkalis, salt and other corrosive media.
2. Oil and gas industry: Used for wellhead equipment, pipeline connectors, valves, pumps . Its corrosion resistance and high temperature performance to adapt to the harsh environment of the oil and gas fields.
3. Electric power industry: used in the manufacture of boiler parts, turbine blades, piping systems. Its high temperature strength and corrosion resistance can meet the strict requirements of power production .
4. Machinery Manufacturing Industry: It can be used to manufacture key parts of machinery and equipment. Such as gears, shafts, bearing housings .
Second, the field of transportation
1. Automobile manufacturing: used in the manufacture of engine components, exhaust systems, braking systems. Such as stainless steel exhaust manifold can withstand high temperature. exhaust gas wash and corrosion resistance.
2. Rail transportation: used in train bodies, bogies, braking systems and other components. High strength, corrosion resistance and good welding performance makes it an ideal material for rail transportation vehicle manufacturing.
3. Ship building: used to manufacture hull structural components, propulsion systems, piping systems. Corrosion resistance can resist seawater erosion, to ensure the long-term use of ships in the marine environment. Stainless steel propeller is resistant to seawater corrosion and high strength.
Third, the field of construction
1. Architectural decoration: manufacture of railings, handrails, sculptures, curtain wall fittings and so on. Beautiful, corrosion-resistant and easy to clean.
2. Building structure: in large-span bridges, high-rise building support structures and other parts.
Fourth, food and medicine field
1. Food processing: used in the manufacture of food processing equipment. Such as storage tanks, agitators, conveying pipelines, valves and so on.
2. Pharmaceutical manufacturing: used in the manufacture of pharmaceutical equipment, medical equipment, etc..
Other fields
1. Environmental protection equipment. manufacturing sewage treatment equipment, exhaust gas treatment equipment. Such as stainless steel sewage pump.
2. Energy field. in the solar energy, wind energy . Such as in solar water heaters, wind generators and connectors .
The Grade for Stainless Steel Casting
JC Casting has experience pouring a wide variety of stainless steel investment casts. Here, we listed the most common stainless steel grade alloys we have poured below. If you need we can provide the Specific material chemistry and mechanical specifications.
300 Series Stainless Steel Casting Alloys
Austenitic 300 series stainless steel is a nonmagnetic chromium-nickel alloy. These stainless steel casting alloys are known for their excellent corrosion resistance. but they cannot gain strength through heat treatment. SS 304L and SS 316L alloys also resist corrosion caused by welding and other high-temperature finishing processes. 300 series alloys are commonly used to invest cast piping and housings for industries. Including medical, marine, food and dairy. We provide a range of 300 series stainless steel casting alloys including:
· 302
· 303
· 304
· 304-L
· 310
· 312
· 316
· 316-L
· 319
· 330
· 347
· BS-3146
· Nitronic 50
400 Series Stainless Steel Casting Alloys
Martensitic 400 series stainless steel is a chromium-magnesium alloy. It provides high strength and machinability. This type of stainless steel is magnetic. It can be hardened through quench and tempering to produce high strength. 400 series is frequently used for investment casting machine parts and valves for automotive and agriculture applications. We offer the following alloys:
· 410
· 416
· 418
· 420C
· 430
· 436
· 440A
· 440C
Precipitation Hardening Stainless Steel Casting Alloys
Precipitation hardening alloys provide high strength and corrosion resistance. They are magnetic and can be heat treated and aged to achieve the strength properties of martensitic steels while maintaining corrosion resistance. Precipitation hardening investment casting alloys are widely used by the military and in aerospace and petrochemical applications. We provide PH stainless steel castings using the following alloys:
· PH 15-5
· PH 17-4
· CD4MCu (25-5)
Common Cast Stainless Steel Grades and typical usages
Common Grade | Features | Applications |
SS 304 | Austenitic stainless steel with Ni content of more than 8%. Food grade alloy, can be used to cast stainless steel components for both household and commercial applications. It is the most widely used stainless steel casting material. | Food industry, chemical industry, mechanical equipment, pipe industry, automotive industry, Housings, medical, watering, mining, petrochemical. |
SS 316 | SS316 is the second most common austenite steel. It is used mainly to increase resistance to corrosion. The Ni content is more than 10%. It has better corrosion resistance than 304 stainless steel castings. 316 stainless steel castings are better suited for the marine environment with harsh air conditions or chemical materials. | Fire fighting, auto parts, marine hardwares, chemical, pipeline, construction, decoration, food industry, etc Housings, gears, plates automotive, food & dairy and petrochemical environments. |
SS 304L / 316L | The mechanical properties are close to those of ss 304 and 316 materials. “L” represents lower carbon content. The material is more ductile. has good welding performance, and has more reliable corrosion resistance. The price is higher than that of materials of the same grade. | Food, chemical, medical, plumbing, medical, petrochemical |
SS 410 / 416 | Series 400 belongs to martensitic stainless steel. High strength, good processing performance and high heat treatment hardness, and does not contain Ni, so the corrosion resistance is weak. They will tend to break rather than bend under intense pressure. | Automotive parts, food & dairy, machine tools, knives, Housings, bushings, handles, brackets |
PH 17-4 | Most common precipitation-hardening martensitic stainless steel. Its content is about 17% chromium and 4% nickel. good corrosion resistance. 17-4 is the strongest of the stainless steel family. Usually used for products and components that are not prone to deformation. | Military, medical, mechanical components, machine tools, turbine blades,ods, pins, links, arms. |
2205 Duplex | Duplex stainless steel 2205 is composite stainless steel consisting of 22% chromium, 2.5% molybdenum, 4.5% nickel-nitrogen. Used for its good mechanical properties and excellent corrosion resistance properties. | Sporting, pump & valve industry. |
Chemical Compositions
Grades | C | Si | Mn | S | P | Cr | Ni | Mo |
304 | ≤0.08 | ≤1.00 | ≤2.00 | ≤0.03 | ≤0.045 | 18 ~ 20 | 8 ~ 11 | – |
304L | ≤0.03 | ≤1.00 | ≤2.00 | ≤0.03 | ≤0.035 | 18 ~ 20 | 8 ~ 12 | – |
316 | ≤0.08 | ≤1.00 | ≤2.00 | ≤0.03 | ≤0.045 | 16 ~ 18 | 10 ~ 14 | 2 ~ 3 |
316L | ≤0.03 | ≤1.00 | ≤2.00 | ≤0.03 | ≤0.045 | 16 ~ 18 | 10 ~ 14 | 2 ~ 3 |
410 | ≤0.03 | ≤1.00 | ≤1.00 | ≤0.03 | ≤0.040 | 11 ~ 13.5 | ≤0.6 | – |
416 | ≤0.15 | ≤1.00 | ≤1.25 | ≤0.15 | ≤0.060 | 12 ~ 14 | ≤0.6 | – |
17-4 ph | ≤0.07 | ≤1.00 | ≤1.00 | ≤0.03 | ≤0.040 | 15.5 ~ 17.5 | 3 ~ 5 | – |
2205 | ≤0.03 | ≤1.00 | ≤2.00 | ≤0.03 | ≤0.040 | 21 ~ 24 | 4.5 ~ 6.5 | 2.5 ~ 3.5 |
More information is on the introduction of How Many Stainless Steel Grades
How to cast the Stainless Steel investment casting
Stainless Steel Investment Casting Process
1. Make Wax Model
Once the mold is finished, inject wax material into the mold cavity.We get a wax model from the mold after cooling. 2. Repair the wax model
2. Repairing wax model
Repair some appearance defects of wax models. Such as slot, wax injection nozzle, flow pattern.
3. Assembly
After inspection wax models, weld them to the casting system one by one to form an assembly. It looks like a tree.
4. Shell Making
The shell-making process is a whole silica sol process. It is to dip the assembly into a good colloidal silica coating. sprinkle with fire-resistant sand. dry and harden shell under certain temperatures. Thus to form dense refractory coating surface outside the surface of wax models.
Then repeat steps 5-6 times. Finally form a certain strength and refractoriness of silica sol shell.
5. Dewaxing
Dewaxing is a process in which the wax inside the shell is melted by high-temperature steam. Then drain out the melted wax. To get a cavity that can be poured into the mold.
6. Pouring
Melted stainless steel ingots into liquid status under a certain high temperature. Then pour the liquid into the shell and cool under room temperature.
Shell Knocking After solidification, knock out the Shell and clean sand .
7. Cutting, Grinding
Cut the stainless steel casting blanks from assembly one by one. Remove the sprue gate by grinding machine. Smooth the surface by various surface finishes. Such as shot blasting, sandblasting, electropolishing, mirror polishing.
8. Inspection
After finishing production, inspection is also an indispensable process before delivery. The stainless steel castings inspection includes dimensional inspection, defects inspection and material inspection. Only qualified products can be shipped to customers.
Post Treatments of Stainless Steel Casting
After Stainless Steel Casting is finished,it will be deep processing. That is the Post Treatments of Stainless Steel Casting. In JC Casting, our main Post Treatments include:
- Heat Treatment: Solution Treatment
- Post Machining
- Surface Finish
Heat Treatment: Solution Treatment
Heat Treatment: Solution TreatmentSolution treatment is a kind of heat-treatment process.
In heating processing, stainless steel castings are heated to a high temperature and maintained at constant temperature in the single-phase zone.
So that the excess phase is fully dissolved into the solid solution. Then cooled rapidly. Finally, we get the su-saturated solid solution.
Unlike heat treatment for other steel investment castings, solution treatment is the only heat treatment method for the stainless steel investment casting process.
The purpose of solution treatment is mainly used to eliminate internal stress. And improve the stainless steel components’ mechanical properties. (e.g. corrosion resistance, ductility, or hardness). It can make the post-machining be easier.
PS:
Before stainless steel castings solution treating operation, casting blank surface cleaning is necessary. Such as removing oils, grease, and other types of residue. Because during stainless steel casting heat treating, The surface leftover may occur degrading the corrosion resistance or other properties of the products.
Post Machining
Investment casting is the primary method for stainless steel parts production. It can create near-net shape products. even without secondary machining.But it does not mean machining can be saved for all the stainless steel cast products.
when there is a closer tolerance and surface finish requirement that casting can not reach. Post Machining will have to be used. We can remove excess material by grinding, milling, drilling. We also have our own CNC Center. CNC machining is the most precise machining process. But the cost is high.
After machining, quality Inspection is also very critical. we use manual inspection equipment and gages as well as the latest in coordinate measuring machine (CMM) technology to measure and record all the dimensions. This ensures our customers always get the quality they want.
Surface Finishes
For stainless steel casting, there are several surface treatment methods to improve its appearance qualtiy. It includes shot blasting, sandblasting, electropolishing, mirror polishing, powder coating.
Shot Blasting
The most common and Low-cost surface finish method. It can remove casting surface mill scales, burrs. It is the process to smooth stainless steel castings by the grinding of small steel balls in a shot blasting machine.
Sand Blasting
The process of cleaning the stainless steel casting surface by the impact of high-speed sand flow. The surface is more smooth than that of sand casting. But the cost is higher.
Electropolishing
Take stainless steel castings as the anode for electrolysis. It is used in an appropriate electrolyte to remove its rough surface. It can improve its surface smoothness. The surface becomes a bit bright after electropolishing.
Mirror Polishing
It is the manual polishing process operated with a grinding wheel. After finishing, the casting surface will look very shining like a mirror. This treatment is the most time costing surface finish method. Mirror Polishing is only suitable for outside areas of stainless steel castings.
Powder Coating:
A surface treatment method for spraying plastic powder onto stainless steel castings. Like painting, there are different colors selected.
Glass Bead Blasting
Glass bead blasting method to refine the surface of stainless steel castings. The surface smooth of sand glass bead blasting looks better than shot blasting. But the cost is higher.
Brush Finishing
A brushed finish typically has a uni-directional satin finish. The brushing gives cast stainless steel parts a distinct look. It retains parts metallic luster and is given a pattern of very fine lines parallel to the brushing direction.
Pickling & Passivation
Pickling is a chemical treatment way to eliminate surface dirt like oxide skin, rust, welding spots. Passivation is a process that forming a new abundant chromium protective layer. It can improve the anti-oxidation ability of stainless steel castings.
China Top Stainless Steel Casting Factory
JC Stainless Steel Casting Foundry is one of the largest casting and machining companies in China. We have our own foundry and CNC Center workshop. The customized stainless steel castings range can be from 0.03kg-100kgs. The raw materials can cover all stainless steel grades.
Why Choose JC Casting?
JC Casting has been the most reliable one-stop source for stainless steel castings. With The competitive prices and full services of stainless steel castings, we have exported our goods to Japan, US, UK, Canada, Australia, South Africa market. If you have any stainless steel casting inquiries, contact us freely. You will get a prompt reply within 6 hours.
JC Casting Featured Stainless Steel Casting Products