Table of Contents
What Is Steel Casting?
Steel casting is a specialized form of casting. Liquid steel is poured into molds to produce solid metal objects. These molds are shaped to meet the specific design needs of the product being manufactured. Steel castings can be made from many of the same carbon and alloy steels as wrought metals. They are one of the most common categories of cast materials in the world.
Types of steel casting
The common types of steel casting are stainless steel casting, carbon steel casting and alloy steel casting.
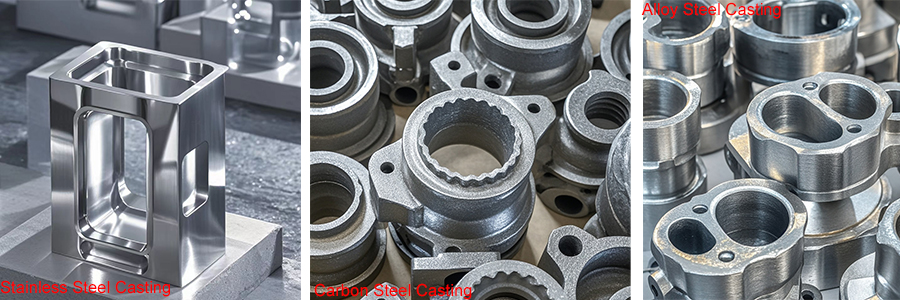
Custom Steel Casting Factory
JC Casting is a Custom Metal Casting Factory with our foundry. If you have any inquiries about the steel casting part, email us!
The advantages of steel casting
1. Super high design flexibility:
– You can freely choose the shape and size of castings. It can make really complex products, even ones with hollow parts. For example, some mechanical parts with super complicated insides and weird sculptures can all be made with steel casting.
– It’s easy to shape and changing the shape isn’t too hard. Turning design drawings into finished products is really fast. You can adjust production quickly according to what you need. This shortens the product development cycle and delivery time.
2. Really strong adaptability in metallurgical manufacturing:
– You can pick different chemical compositions and microstructure controls to meet all kinds of engineering needs. By adjusting the alloy elements in molten steel, you can get steel castings with different characteristics to fit different working environments and conditions.
– Through different heat treatment processes, you can choose mechanical properties and how it works in a wide range. For instance, quenching and tempering can make the steel castings stronger, tougher and better for processing and welding.
3. High overall structural strength:
– Steel castings are naturally strong and can handle big loads and stresses. They’re widely used in places that need a lot of strength, like heavy machinery and building structures.
– The steel casting material is the same in all directions, so the performance is even everywhere. The overall structure is solid, making engineering more reliable and safe.
4. A wide range of weights:
Small steel castings can weigh just a few dozen grams, while big ones can be tons, dozens of tons or even hundreds of tons. It can meet different size and weight needs for projects.
5. Good welding performance:
Steel castings are great for welding. You can easily weld them to other steel parts to make bigger and more complex structures. Compared to some other casting materials, steel casting is better for assembly and later processing because of its welding ability.
6. Good corrosion resistance
Some special steel casting materials, like stainless steel castings, are good at resisting corrosion. They can be used in harsh environments like chemical and marine engineering.
The applications of steel castings
Steel castings have a wide range of uses. The following are six main uses and examples:
1. In the field of mechanical manufacturing:
- Manufacturing heavy machinery parts: For example, hooks of large cranes and large gears. These parts need to bear huge weights and stresses. The high strength and good toughness of steel castings can meet the requirements. For example, at port terminals, the hooks of large cranes bear the lifting tension of heavy objects for a long time. The material characteristics of steel castings can ensure their safe and reliable operation.
- Producing machine tool components: Basic components such as the bed and column of machine tools require high precision and stability. Steel castings can be manufactured through precision casting processes to ensure the stability and precision retention of machine tools during high-speed and high-precision machining. For example, the beds of some high-precision machining centers are made of steel castings. It can reduce the vibration of the machine tool during operation and improve the machining accuracy.
2. Construction industry:
- Building structural components: Such as steel beams and columns in steel structure buildings. Steel castings can be customized into steel beams and columns of various shapes and sizes according to the requirements of architectural design to meet the needs of different building structures. For example, large stadiums and high-rise buildings.
- Architectural decorative parts: Such as sculptures, railings, decorative panels, etc. of buildings. Steel castings can be manufactured into various exquisite shapes and patterns through casting processes to add artistic beauty to buildings. For example, urban landmark buildings.
3. Energy field:
- Petrochemical equipment components: Such as drill pipe joints, valves, pipe connectors, etc. These components need to be used for a long time in harsh working environments. The corrosion resistance, wear resistance and high strength characteristics of steel castings can ensure their reliability in the petrochemical field. For example, on offshore oil drilling platforms, the valves of steel castings can withstand high-pressure and highly corrosive working environments to ensure the normal exploitation and transportation of oil.
- Power equipment components: Such as superheaters, reheaters, and steam turbine blades in power station boilers. These components need to work in high-temperature and high-pressure environments. The high-temperature resistance and good mechanical properties of steel castings can meet the requirements of power equipment. For example, steam turbine blades of thermal power stations.
4. Transportation field:
- Automobile manufacturing: Key parts in automobiles, such as engine blocks, transmission cases, steering knuckles, etc. can be manufactured by steel castings. The high strength and good wear resistance of steel castings can meet the use requirements of automobiles. For example, for high-performance racing engine blocks, steel castings are usually used to withstand higher pressure and temperature.
- Rail transit: Such as train wheels, axles, brake system components, etc. These parts need to have high strength, high toughness and good wear resistance. Steel castings can meet the special requirements of rail transit. For example, the axles of high-speed trains.
5. Mining machinery field:
- Mining equipment components: Such as jaw plates of jaw crushers, crushing walls of cone crushers, liners of ball mills, etc. These parts need to withstand huge impacts and wear during the mining process. Steel castings have high hardness and good toughness.
- Mining transportation equipment components: Such as the carriage and frame of mining dump trucks. The requirements for the strength and wear resistance of components are very high. Steel castings can meet these requirements.
6. Shipbuilding field:
- Ship engine components: Such as the cylinder block, piston, crankshaft, etc. of ship engines. These parts need to work in high-temperature, high-pressure and highly corrosive environments. The high-temperature resistance, corrosion resistance and high strength characteristics of steel castings can meet the requirements of ship engines.
- Ship structural parts: Such as keels, ribs, deck connectors, etc. of ship hulls. Steel castings can manufacture ship structural parts with complex shapes and precise dimensions to ensure the structural strength and stability of ships. For example, large luxury cruise ships.
The steel castings process
The processes of steel castings mainly include the following:
- Sand casting:
– Green sand casting:
Using green sand as the molding material has the advantages of low cost and high production efficiency. It is suitable for producing medium and large steel castings. But, steel castings made with green sand are prone to defects such as porosity and sand inclusion. Thus, higher requirements are imposed on the quality of molding sand and the molding process. For example, construction and machine bases .
– Dry sand casting:
The molding sand is dried before molding. The sand mold has better strength and permeability. it can effectively reduce defects such as porosity and sand inclusion in steel castings. But, dry sand casting has a longer production cycle and relatively higher cost. It is often used to produce steel castings with higher quality requirements.
– Sodium silicate sand casting:
Sodium silicate is added to the molding sand as a binder, which can improve the strength and collapsibility of the molding sand. The sodium silicate sand casting process is simple to operate and has high production efficiency. However, when a large amount of sodium silicate is added, it is relatively difficult to recycle and reuse the used sand.
– Resin sand casting:
Using resin as a binder has the advantages of high strength, good collapsibility, and high dimensional accuracy. It can produce steel castings with complex shapes and high precision. The gas evolution of resin sand is relatively low, which is conducive to reducing porosity defects in steel castings. This process is widely used in the production of steel castings. Especially for some parts with higher quality and precision requirements. Such as machine tool beds and engine blocks.
2. Investment casting (lost wax casting):
First, make a mold for the casting with materials such as paraffin or foam plastic. Coat the surface of the mold with refractory materials. Then heat the mold to melt and discharge the paraffin or foam plastic, forming a hollow mold. Finally, pour molten steel into the mold. After the molten steel cools and solidifies, remove the refractory materials to get the steel casting. Investment casting can produce steel castings with complex shapes, high dimensional accuracy, and good surface quality. But, the process is complex and costly. It is suitable for producing small and precise steel castings. Such as parts in the aerospace field and medical device parts.
3. Lost foam casting:
Like investment casting, a model is also made first. But the model material used is expandable polystyrene (EPS) or other foam plastics. Bury the model in casting sand, and then pour molten steel. The model gasifies and disappears, and the molten steel occupies the position of the model and cools and solidifies to get the steel casting. Lost foam casting has the advantages of simple process, high production efficiency, low cost, and high precision. It is suitable for producing steel castings with complex shapes and large batches, such as automotive parts and pipe fittings.
China Custom Steel Casting Foundry –JC Casting
C Casting Custom Steel Casting Foundry stands out as a reliable and innovative player. As a Steel casting foundry in China. We offter advanced technology and skilled craftsmanship, it offers high-quality steel castings . From heavy machinery components to intricate architectural elements, the foundry’s capabilities are extensive. Its commitment to precision and durability ensures that each casting meets the highest standards. No matter in domestic or international markets, China JC Custom Steel Casting Foundry is a trusted name.